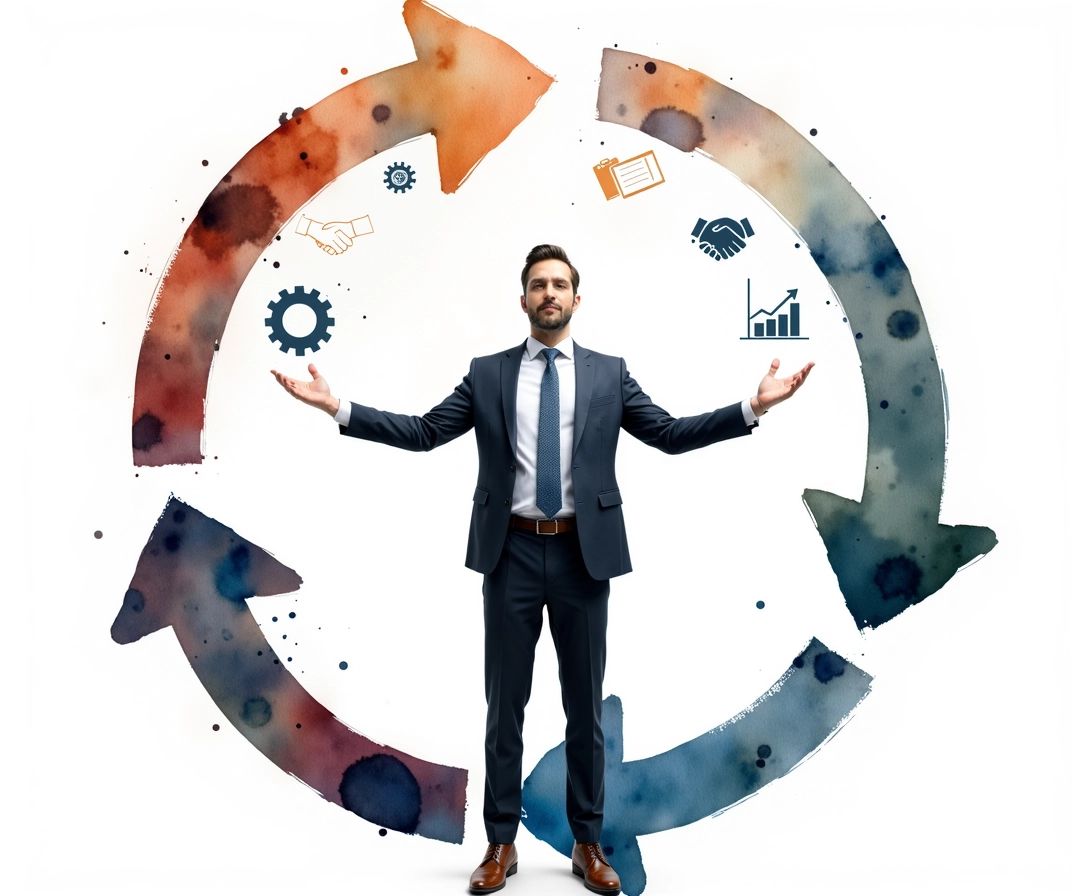
Total Quality Management Explained: Principles, Benefits, and Implementation
Introduction to TQM
Total quality management (TQM) is a business approach that prioritizes constant improvement in every aspect of a company's activities. It's like a company-wide mentality focused on delivering the best possible products and services to customers.
Rather than simply checking for product defects at the end of production, TQM aims to incorporate quality into every process stage. It emphasizes involving everyone in the organization, from upper management to frontline workers, in this quest for excellence.
TQM became well-known in the 1980s, inspired by the achievements of Japanese manufacturers who adopted this method. They saw remarkable enhancements in their products' quality while reducing expenses. This success story had a ripple effect across the global market, leading to the broad adoption of TQM principles in various industries.
While alternative quality management methods have emerged since then, TQM's fundamental principles remain applicable. Its focus on customer satisfaction, ongoing improvement, and employee engagement endures as foundations of current quality management strategies.
Key Principles of TQM
To grasp TQM fully, we need to examine its main principles. These principles are TQM's foundation, directing companies toward a culture of continuous enhancement and customer contentment. Let's explore:
Customer Focus
TQM prioritizes the customer above all else. It acknowledges that fulfilling and exceeding customer requirements is crucial for success. This entails understanding their needs, desires, and anticipating their future demands.
Total Employee Involvement
TQM isn't just for managers; it relies on every employee's active engagement. Everyone, from executives to frontline staff, contributes to finding areas for improvement and implementing solutions. This nurtures a sense of responsibility for quality across the company.
Process-Centered Approach
TQM perceives a company as a network of interconnected processes. By improving these processes, businesses can simplify operations, reduce mistakes, and enhance efficiency. This requires constant analysis, refinement, and betterment of work processes.
Integrated System
TQM underscores the need for a unified strategy. All divisions, processes, and individuals should collaborate toward shared quality objectives. This integrated system guarantees everyone is in sync and striving for the same targets.
Strategic and Systematic Approach
Implementing TQM isn't random. It demands a defined strategy, transparent objectives, and a systematic execution approach. Careful preparation, resource allocation, and performance evaluation are crucial aspects of this principle.
Continual Improvement
At the heart of TQM is "Kaizen" – a Japanese word meaning continuous improvement. Maintaining quality isn't enough; TQM aims for ongoing enhancement of products, services, and procedures. This involves promoting a culture of learning, innovation, and adaptation.
Fact-Based Decision Making
While intuition has its place, TQM emphasizes data-informed choices. By gathering and studying quality-related data, companies can gain insights into their performance, pinpoint improvement areas, and objectively monitor progress.
Open Communication
Effective communication is vital for TQM. Transparency, open discussions, and active listening are essential for sharing insights, promoting collaboration, and ensuring everyone is informed and aligned with quality endeavors.
Implementation Process
Having discussed the fundamental principles, let's examine how to put TQM into practice. Implementing TQM is a continuous journey, not a quick fix. It requires a structured method, complete commitment, and a company-wide dedication to change.
1. Build a Foundation of Commitment
TQM can't be imposed; it requires buy-in from everyone. Start by conveying the advantages and securing upper management's unwavering support. This top-down commitment is vital for allocating funds, establishing clear expectations, and cultivating a culture open to change.
2. Define Your Quality Goals
What constitutes success for your company regarding quality? Set clear, quantifiable, and attainable quality targets aligned with your overall business strategy. These targets will guide you throughout TQM implementation.
3. Map Your Processes
TQM revolves around understanding and optimizing work processes. Outline your essential procedures, identifying critical steps, potential hurdles, and areas for enhancement. This detailed process study will be the basis for streamlining operations and elevating quality.
4. Empower Your People
TQM thrives on employee participation. Offer the necessary training and tools to equip your team with the abilities and knowledge to contribute to quality improvement projects. This empowerment fosters a feeling of ownership and accountability for quality at every level.
5. Implement and Monitor
Put your TQM strategy into action, beginning with a trial project in a specific area or department. This lets you experiment, gather feedback, and adjust your approach before full-scale implementation. Continuously track your advancement, measure key metrics, and make adjustments when necessary.
6. Foster a Culture of Continuous Improvement
TQM is not a destination; it's an ongoing journey. Encourage a culture where constant improvement becomes ingrained. Acknowledge successes, learn from setbacks, and cultivate an environment of open communication, feedback, and creativity. This ensures that TQM becomes a core part of your company's identity.
Keep in mind that TQM implementation is an investment – in your workforce, processes, and ultimately, your future achievements. By embracing its principles and adopting a structured method, you can transform your company into a model of quality and customer satisfaction.
Tools and Techniques
TQM in action means employing specific tools and methods to propel ongoing improvement. These tools aren't just trendy terms; they're practical techniques for examining processes, identifying issues, and implementing solutions. Let's explore some widely used TQM tools:
1. PDCA Cycle (Plan-Do-Check-Act)
This cyclical process is fundamental to TQM. It offers a structured framework for constant enhancement, ensuring systematic and effective implementation of changes.
- Plan: Pinpoint an improvement opportunity and create a plan to address it.
- Do: Execute the plan on a small scale, collecting data and feedback.
- Check: Analyze the implementation outcomes, comparing them to your anticipated results.
- Act: If positive, implement the change more broadly. If not, modify your plan and retry.
This iterative method allows for adjustments along the way, ensuring continuous optimization of improvement efforts.
2. Pareto Chart
This bar graph visually presents the occurrence frequency of different issues or defect causes. By prioritizing enhancement efforts based on the most significant contributors to quality problems, companies can focus resources where they'll have the biggest impact.
3. Cause-and-Effect Diagram (Fishbone Diagram)
This visual tool aids teams in brainstorming and pinpointing potential causes of a specific problem. By sorting potential causes into distinct branches, the diagram offers a structured way to analyze complex issues and identify root causes.
4. Check Sheets
These straightforward yet effective tools are used for standardized data collection. Whether tracking defects, customer grievances, or process deviations, check sheets provide a visual data representation, simplifying the identification of patterns.
5. Histograms
These graphical depictions of data distribution help visualize the frequency of different values within a dataset. This allows teams to see the variation range in a process, spot potential outliers, and understand the data's central tendency.
6. Control Charts
These charts monitor a process over time, helping determine its stability and predictability. By plotting data points against upper and lower control limits, teams can quickly identify process deviations from the expected range, signaling a need for investigation and potential corrective measures.
7. Scatter Diagrams
These graphs plot the relationship between two variables, helping to identify correlations or patterns. This can be particularly helpful in understanding how changes in one variable might affect another, for example, the link between training hours and defect rates.
8. Flowcharts
These visual process representations, using symbols to depict steps and their sequence, help identify potential bottlenecks, redundancies, or areas for improvement. Flowcharts offer a clear understanding of process operations, making analysis and optimization easier.
By adopting these tools and techniques, companies can shift TQM from theory to a practical, results-driven approach. Remember, the key is selecting the right tools for your specific needs and consistently using them to drive meaningful improvements.
Benefits and Challenges
Embracing TQM can bring numerous advantages, but like any significant organizational change, it presents challenges. Understanding both sides is crucial for successful implementation and reaping the rewards of a quality-focused culture.
Advantages of TQM
- Enhanced Customer Satisfaction: By prioritizing the customer, TQM results in products and services that consistently meet or surpass expectations, building loyalty and positive feedback.
- Improved Process Efficiency: TQM's emphasis on process optimization streamlines operations, reduces waste, minimizes errors, and ultimately enhances productivity and cost-effectiveness.
- Increased Employee Engagement: TQM empowers employees at all levels to contribute to quality improvement, fostering a sense of ownership, pride, and a more collaborative and engaged workforce.
- Data-Driven Decision Making: TQM stresses data analysis for identifying improvement areas and tracking progress, leading to more informed and effective decision-making.
- Continuous Improvement Culture: TQM embeds a mindset of constant improvement, fostering innovation, adaptability, and a proactive problem-solving approach, keeping companies agile and competitive.
Potential Challenges
- Resistance to Change: Implementing TQM demands a significant cultural shift, and resistance from employees used to established practices can hinder progress.
- Time and Resource Commitment: TQM is a long-term endeavor requiring sustained commitment, dedicated resources, and ongoing training, which can strain budgets and test patience.
- Maintaining Momentum: Initial enthusiasm for TQM can diminish. Sustaining momentum, celebrating achievements, and constantly reinforcing the importance of quality is vital to prevent backsliding.
- Effective Communication is Key: Open and transparent communication is crucial for TQM's success, ensuring everyone understands their roles, goals, and progress to maintain alignment and support.
- Measuring ROI: Quantifying TQM's return on investment can be difficult, requiring a strategic approach to data collection and analysis to demonstrate the tangible benefits of a quality-focused culture.
Overcoming these challenges requires strong leadership, clear communication, and a firm commitment to TQM principles. However, the potential rewards – higher customer satisfaction, improved efficiency, and a more engaged workforce – make it a worthy investment.
Real-world Success Stories
The best way to understand TQM's power is through real-life examples. Numerous companies across industries have successfully implemented TQM principles, achieving remarkable outcomes. Let's explore some compelling instances:
Toyota's Production Revolution
Toyota's well-known production system, often called "lean manufacturing," is rooted in TQM. By adopting principles like continuous improvement (Kaizen), employee involvement, and waste reduction, Toyota transformed the automotive industry. Their dedication to quality led to superior vehicles, lower production costs, and increased customer satisfaction, setting a global standard for manufacturing excellence.
Xerox's Quality Transformation
Facing stiff competition in the 1980s, Xerox embarked on a TQM journey to revitalize its operations. They adopted a customer-focused approach, empowering employees to identify and address quality issues. Through rigorous process enhancements, they significantly reduced defects, lowered costs, and boosted customer satisfaction, regaining market share and solidifying their position as a leader in the copier industry.
Ford Motor Company's Turnaround
In the early 1980s, Ford faced a crisis. Quality problems plagued their vehicles, causing declining sales and customer trust. Inspired by Japanese automakers' TQM success, Ford implemented a company-wide quality initiative. They focused on better product design, enhanced manufacturing, and fostering a quality-driven culture. The outcome? Ford significantly improved vehicle quality, regained customer confidence, and achieved a remarkable turnaround.
These success stories demonstrate that TQM is more than just a theoretical framework—it's a powerful method for achieving enduring success. By adopting its principles, organizations can transform their operations, satisfy their customers, and gain a significant competitive edge.
Ready to unlock your organization's full potential with data-driven innovation? Discover how Derisky.ai empowers businesses to make smarter decisions, minimize risk, and maximize their innovation ROI. Visit our website at https://derisky.ai today!